Difference between PC and PLC-based automation
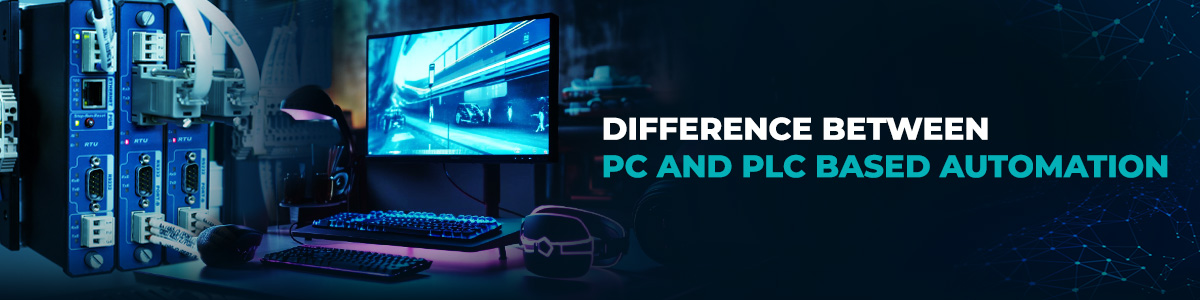
The industrial world has progressively reduced manual involvement to boost productivity and efficiency. While automation is a modern buzzword, industrial transformation has long been driven by mechanization. Turnkey automation emerged in the 1920s with electromagnetic relays and switches, streamlining assembly lines and reducing manual tasks. However, it was the mass production of programmable logic controllers (PLCs) in the late 1960s and early 1970s that truly highlighted the advantages of turnkey automation in industrial processes.
The severely constrained functional scope, coupled with the logistical difficulties associated with the electromagnetic relays and switches – they were overly large and hard to reconfigure – had restricted their application in the industrial sector. However, a PLC-based automation system, which could be integrated with other hardware equipment, besides being developed to perform a number of electromechanical processes, prompted its widespread adoption by industries across sectors. Among the many advantages of a PLC-based system was that it could be reprogrammed and reconfigured more easily, besides its extensive functional scope.
Notwithstanding the many advantages of the PLC-based automation system, there are limitations that restrict its application in industries that require more complex platforms. These include the pharmaceutical and semiconductor fabrication industries, where the higher degree of flexibility and accuracy that a Personal Computer (PC)-based automation system offer ensure more efficient operations. By dint of the fact that they can be programmed with sophisticated languages, the PC-based automation system can be designed, and developed to perform an entire sequence of complex operations. The future of PC-based automation systems seems bright as attempts are under way to overcome some of the limitations of the computer, and trends indicate that they might replace PLC-based control systems in several industries.
PLC-based automation systems
A PLC is essentially a miniature and ruggedized version of a PC, albeit without the latter’s diverse functional scope nor its ability to perform complex operations. However, the PLC was never conceived for such purposes. Ever since it was first invented, in the late 1960s, the PLC was designed and built to function in physically punishing conditions. Such an environment is characterized by extremities of temperature, pressure, and volatile physical conditions. PLC-based automation systems continue to be extensively used on-site at oil rigs, power plants, and even at mining sites. Unlike a general-purpose PC, a PLC is built to perform either a specific task or a sequence of tasks, mostly of an electromechanical nature.
From the time that the PLC became commercially available in the 1970s, control systems powered by the device became a preferred component in industrial assembly lines. This was primarily owing to the advantages that they offered over their predecessors, the electromagnetic relays. Some of these advantages include
• Rapid scanning time – a thousandth of a second
• Ability to perform successive operations in the stipulated sequence
• Ability to respond to real-time changes
• Assured boost to productivity and efficiency
The electromagnetic relay was essentially just a switch, which meant that it could only turn operations on or off, or ensure that functional blocks are switched on and off in a particular sequence. However, the relay’s lack of functional flexibility meant that the hardware had to be entirely reconstituted when they had to perform a different task. The PLC-based automation system, on the other hand, only needed to be reprogrammed using ‘Ladder Logic’. Furthermore, the PLC-based control system can be very effectively deployed to run an automated assembly line; a PLC-based automation system is programmed to ensure that a number of operations in the assembly line follow each other according to a pre-determined sequence.
A PLC-based automation system can be an intricate network of diverse sensors, measurement devices, supervising each of them, and, further ensuring each of these devices works in perfect concert with each other. Perhaps the best illustration of the efficiency that a PLC-based control system lends to a production plant is on an oil rig. Given that the conditions on an oil rig are very obviously hazardous, there can be no room for error in measurement. And a PLC-based system tasked with measurement of pressure in a pipeline, say, can ensure that alerts are sounded without delay when the pressure exceeds the prescribed safety level. Similarly, a PLC-based control system, acting on a reading of a measurement device integrated into the production set-up, can use the number as an input to trigger another process that is part of the production cycle. Sensor-based operations can, furthermore, ensure that either separate functional blocks or the entire assembly line is turned off in the event of violations of safety standards.
• 90% reduction in power consumption
• They boast in-built troubleshooting and diagnostic features
• Precision and efficiency in performance of repetitive tasks
These are among some of the more salient benefits that enterprises can accrue of by integrating PLC-based automation systems with their existing production lines. Above all else, a PLC-based system’s ability to respond to altered environmental or mechanical conditions in real-time help create safer working conditions for both machines and the workers. Industries, across sectors, are understandably eager to leverage the capabilities of the PLC-based automation system to drive profits. It is little wonder then that market research agencies forecast a bright future for the PLC market – valued at USD 10 billion in 2023, it is estimated to register a Compound Annual Growth Rate (CAGR) of 10% over the next nine years.
PC-Based Automation Systems
The readily apparent advantages of the PLC-based control system over its predecessor, the electromagnetic relay, notwithstanding, there are several limitations associated with them, owing to which industries have turned to the PC to solve inherently more complex problems that arise during the production cycle. One of the biggest drawbacks of the PLC-based automation system is that it has to be programmed using ‘Ladder Logic’ flowcharts, owing to which uploading code for tasks inherently more complex and intricate becomes cumbersome. However, PC-based automation systems can be coded using sophisticated high-level languages such as C, C++, Java, and Python, all of which can enable a more elegant functional mechanism for the execution of not just one but an entire sequence of elaborately complex tasks.
The biggest limiting factor vis-à-vis the use of the PC in an industrial environment is its inability to withstand harsh physical conditions. This is a limitation that enterprises are striving to overcome through use of ruggedized versions of the consumer-grade PC, which is the Industrial Personal Computer (IPC). Among the advantages that a PC-based automation system boasts over its PLC counterpart include:
• Enabling remote operations
• A PC can be connected to the internet
• Allowing for use of high-level languages
• Ability to interface with multiple systems
• Use of complex algorithms
• A PC’s utility value extends beyond automation
A PLC-based automation system is ill-equipped for use in remote inspection and remote control systems since it cannot be directly connected to the internet. In the Industry 4.0 era, this is a severe limitation considering the fact that industries the world over are in frantically accelerating their digital transformation journeys. The modern-day factory floor is incomplete without the Internet of Things (IoT) devices, smart sensors, and edge computing equipment, the capabilities of which can be optimized with a PC-based automation system.
Consider, for instance, a remote machine vision inspection system. The benefits of this system, powered by a PC, were brought home during the pandemic when technicians and engineers were compelled to work remotely. The machine vision inspection system allows for engineers to test any machine, however complex it might be, from remote sites. Through the use of high-definition cameras, sensors, among other sophisticated devices, engineers can conduct a comprehensive examination of a finished product. What is more, a PC-based control system even allows for the assembly line to be turned off remotely by engineers in the event of any deviation from prescribed safety standards. A PC’s inherently diverse functional portfolio means that its role within the production line need not be restricted to automation of processes. Furthermore, advanced simulation tools such as the ‘Digital Twin’ can more easily be programmed on a PC-based system.
The ‘Digital Twin’ is a virtual replica of either a functional block or the entire factory floor that can be used to run comprehensive tests to enable technicians to identify, and correct, technical snags in the equipment prior to the start of the production process.
• Digital Twin
• Edge computing
• IoT devices
• Predictive Maintenance models
…are among some of the technologies that have come to be identified with Industry 4.0 that can be effectively integrated with the assembly line using a PC-based automation system. And although robotic systems are also used with PLC-based automation system, when integrated with a PC-based control system, they can be deployed for the execution of several complex processes that require coordination and communication with other machinery and tools. These include loading and unloading of heavy machinery on the factory floor, or inventory management, among others. Working in tandem with weight sensors, robots can accurately estimate the number of materials stacked on the factory floor, and each time there is a change in the weight of the stack, the digital inventory reflects either an addition or reduction in the bill of materials.
However, the PC-based automation system is not without its drawbacks. Their relatively lower tolerance for harsh physical conditions means that they need additional hardware to interface with the physical equipment when deployed on-site at power plants, for instance. Notwithstanding these limitations, the use of the PC-based automation system is expected to register a marked increase in the years to come, with the market likely to swell to USD 50.32 billion by 2030.
PC and PLC-based automation at TEAL
At TEAL, we build machines that are inseparable cogs in the larger automated systems that manufacturing firms employ. We are machine builders, and our products power key manufacturing processes across sectors, ranging from automotive to aerospace. While TEAL develops a number of PLC-based automation systems for the manufacturing sector, its PC-based solutions are currently geared towards peripheral operations such as data logging. Many of our turnkey solutions built for the energy sector are powered by PLC-based systems. For instance, our Supervisory Control and Data Acquisition (SCADA) systems, with the PLC at their core, are designed to cater for, among others, the food-and-beverage industry.
Meanwhile, TEAL’s PC-based automation systems are designed to ease use of complex software, besides enabling a number of supplementary operations associated with manufacturing and production. For instance, the operation of an automated assembly line entails collection and analysis of large and diverse data sets requiring PC-based systems. TEAL also boasts an in-house simulation and robotics team dedicated to the development of specialized PC-based automation solutions. TEAL has been a pioneering force in developing robust PC-based control systems, with in-built state-of-the-art software. TEAL has also successfully integrated Industry 4.0 solutions in its PC-based control systems, besides shoring up the capabilities of these systems by integrating with data acquisition and processing abilities.
Frequently Asked Questions