The Future of Automation: Trends and Predictions for 2025
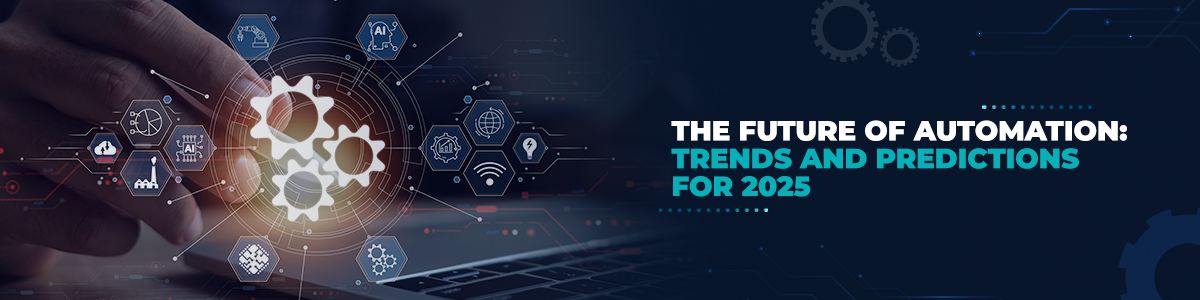
Industrial automation has evolved from simple mechanization to sophisticated, interconnected systems that drive efficiency and innovation across industries. Defined as the use of control systems, such as computers or robots, and information technologies for handling different processes and machinery in an industry, industrial automation has revolutionized how businesses operate. Over the past decade, technological advancements have further propelled this field, enabling industries to achieve unprecedented precision, productivity, and safety levels.
Importance of Understanding Future Trends
As industries continue to embrace automation, staying ahead of emerging trends is not just beneficial—it's essential. Understanding these trends enables businesses to maintain a competitive edge, streamline operations, and unlock new growth opportunities. At Titan Engineering and Automation Limited (TEAL), we are committed to innovation and leadership in industrial automation, continuously exploring new technologies and solutions to meet the evolving needs of our customers.
Current State of Industrial Automation
Recent Developments in Industrial Automation:
Industrial automation has witnessed significant advancements in recent years. Technologies such as Artificial Intelligence (AI), the Internet of Things (IoT), and robotics have been at the forefront of this transformation, increasing efficiency and reducing operational costs. The adoption rates of these technologies have surged, with industries ranging from manufacturing to logistics integrating automation into their core processes, resulting in improved productivity and enhanced product quality.
Key Technologies Driving Today’s Automation
- AI and Machine Learning: AI and machine learning are the core of the latest industrial automation trends. By enabling machines to learn from data and predict outcomes, these technologies are not just about replacing human labor but enhancing human decision-making. For example, AI-driven manufacturing systems can predict equipment failures before they occur, schedule maintenance at the optimal time, and even optimize production schedules based on predictive analytics. This proactive maintenance and production planning approach significantly reduces unplanned downtime and increases overall operational efficiency.
- IoT Integration: Integrating IoT with automation systems has paved the way for a more connected and efficient industrial environment. IoT devices collect real-time data from machinery, production lines, and supply chains, providing invaluable insights into operational performance. This data can be used to optimize processes, reduce waste, and improve energy efficiency. Furthermore, IoT-enabled predictive maintenance systems can monitor equipment health in real-time, predicting failures before they happen and scheduling repairs at the most convenient times, thereby minimizing disruptions to production.
- Robotics and Cobots: Robotics have been a staple of industrial automation for decades, but recent advancements have taken this technology to new heights. The rise of collaborative robots, or cobots, represents a significant shift in how humans and machines interact in the workplace. Unlike traditional industrial robots, which are often confined to cages for safety reasons, cobots are designed to work alongside humans, assisting with tasks that require precision, strength, or endurance. These robots are equipped with advanced sensors and AI, allowing them to navigate complex environments, adapt to changes in real-time, and learn from human workers. This collaboration between humans and robots improves productivity and enhances workplace safety by taking over dangerous or repetitive tasks.
- Edge Computing: Another crucial development in industrial automation is the advent of edge computing. As more devices become interconnected through IoT, the volume of data generated has exploded. Edge computing brings computation and data storage closer to the data source, reducing latency and bandwidth usage. This is particularly important in industrial environments where real-time processing and decision-making are critical. For instance, in a factory setting, edge computing allows for immediate sensor data analysis, enabling rapid adjustments to the production line without sending data back and forth to a central server.
- Cloud-Based Automation Solutions: Cloud computing has transformed automation, making it accessible and scalable. By leveraging the cloud, companies can deploy automation solutions across multiple sites, ensuring consistency and efficiency while reducing the need for costly on-site infrastructure. Cloud-based platforms also enable seamless updates and maintenance, keeping systems current with the latest technological advancements. Additionally, the cloud facilitates collaboration across teams and locations, allowing for a more integrated approach to automation and process management.
- Advanced Sensors and Vision Systems: Using advanced sensors and vision systems in automation is another key growth area. These technologies allow machines to perceive their environment in previously impossible ways. For example, in quality control, vision systems equipped with AI can inspect products at speeds and accuracies far beyond human capabilities, ensuring that only products meeting the highest standards are sent to market. In manufacturing, sensors monitor environmental conditions such as temperature and humidity, adjusting processes in real-time to maintain optimal conditions for production.
These key technologies are driving current automation and laying the foundation for the future. As industries continue to integrate these technologies, we can expect further improvements in efficiency, safety, and overall productivity, positioning companies to meet the challenges of a rapidly evolving market. TEAL remains at the forefront of this technological evolution, constantly exploring innovations to help our customers stay ahead of the curve.
Emerging Trends in Industrial Automation for 2025
Trend 1: Increased Adoption of Artificial Intelligence and Machine Learning
AI and machine learning are poised to take center stage in industrial automation by 2025. These technologies will drive predictive maintenance, where systems anticipate equipment failures before they happen, reducing downtime and extending the lifespan of machinery. Additionally, AI will refine quality control by quickly identifying defects and ensuring only the best products reach the market. Self-healing systems, capable of detecting and correcting faults autonomously, will further enhance efficiency and reliability.
Trend 2: Expansion of Autonomous Systems
Fully autonomous production lines are becoming more common, particularly in industries like automotive and electronics. These systems handle complex tasks with precision, significantly reducing the need for human intervention. Beyond manufacturing, autonomous systems are also transforming logistics, with self-driving vehicles and drones optimizing the supply chain. As these technologies mature, they will be increasingly adopted across various sectors.
Trend 3: Integration of 5G in Industrial Automation
The introduction of 5G technology will revolutionize industrial automation by enabling faster and more reliable communication within factories. This will support the development of smart factories, where real-time data can be used to adjust production processes dynamically. Remote monitoring and control will also become more efficient, allowing for greater flexibility and responsiveness in manufacturing environments.
Trend 4: Human-Machine Collaboration
As automation becomes more prevalent, the role of humans in the workplace will shift toward collaboration with machines. Collaborative robots, or cobots, are designed to work alongside humans, taking on repetitive or hazardous tasks while humans focus on more complex decision-making. This trend will require ongoing workforce training and upskilling to ensure that employees can effectively interact with and leverage these advanced technologies.
Trend 5: Automation as a Service (AaaS)
Automation as a Service (AaaS) is emerging as a flexible and cost-effective solution for companies looking to adopt automation technologies. By offering automation on a subscription basis, AaaS eliminates the need for heavy upfront investments, making it accessible to businesses of all sizes. This model also allows for easy scaling and ensures companies have access to the latest technologies with minimal disruption.
Trend 6: Rise of Sustainable and Green Automation
Sustainable automation solutions are gaining traction as industries strive to reduce their environmental impact. These systems focus on optimizing energy use, minimizing waste, and incorporating sustainable practices into production processes. Companies that adopt green automation will not only reduce their carbon footprint but also meet growing consumer demand for environmentally responsible products.
Predictions for the Future of Industrial Automation
Prediction 1: Universal Standards for Interoperability
As industrial automation industry becomes more complex, the need for universal standards that enable seamless integration across various systems and technologies will become critical. These global standards will ensure that different automation systems—regardless of the manufacturer or platform—can communicate and work together harmoniously. This will simplify the integration process, reduce implementation costs, and allow for more flexible, scalable automation solutions. Additionally, standardization will foster innovation, as companies can build upon a common framework, making it easier to adopt new technologies and enhance existing systems without compatibility concerns.
Prediction 2: Widespread Use of Digital Twins
Digital twins, which are virtual replicas of physical assets, will become a cornerstone of industrial automation by 2025. These digital models will enable manufacturers to simulate, monitor, and optimize processes in real-time, offering unprecedented insights into operations. For example, a digital twin of a production line can predict potential failures before they occur, allowing for preventative maintenance that minimizes downtime. Moreover, digital twins will facilitate rapid prototyping and testing, enabling companies to explore new production methods or equipment configurations without the risks and costs associated with physical trials. As a result, businesses will achieve higher efficiency, reduced costs, and improved product quality.
Prediction 3: Enhanced Cybersecurity Measures
With the increasing connectivity of automation systems, cybersecurity will become a top priority for industrial companies. As more devices and systems are interconnected, the risk of cyberattacks grows, making it essential to protect critical infrastructure. Future cybersecurity measures will likely involve predictive approaches, where AI and machine learning are used to detect anomalies and potential threats before they can cause harm. This proactive stance will be essential in safeguarding automated systems, particularly in industries where disruptions could have severe consequences, such as energy, healthcare, and manufacturing. Enhanced cybersecurity protocols will also be integrated into the design of automation systems, ensuring that security is a fundamental aspect of every component and process.
Prediction 4: Enhanced Data Utilization
The future of industrial automation will be increasingly data-driven, with companies leveraging big data analytics to gain deeper insights into their operations. Real-time data collection and analysis will allow businesses to monitor production processes more closely, identify inefficiencies, and make informed decisions that enhance productivity and product quality. Predictive analytics will play a significant role, enabling companies to anticipate trends, adjust operations proactively, and respond swiftly to market changes. Furthermore, data-driven automation will support personalized manufacturing, where products can be customized on a mass scale to meet specific customer needs, offering a significant competitive advantage in a consumer-driven market.
Prediction 5: Customization and Flexibility in Automation Solutions
As industries continue to evolve, there will be a growing demand for automation solutions that are not only effective but also highly customizable. Companies will seek automation systems tailored to their unique operational needs, allowing them to adapt to changing market conditions and consumer demands quickly. This trend will drive the development of modular automation solutions, where systems can be easily reconfigured or expanded as needed. TEAL, with its expertise in creating flexible automation systems, will be at the forefront of this shift, offering solutions that cater to specific industry requirements. This customization will extend beyond hardware, encompassing software solutions that can be adapted to different processes, environments, and regulatory standards.
Challenges and Opportunities in the Future of Automation
Key Challenges to Anticipate
While the future of industrial automation is bright, it is not without its challenges. Understanding and addressing these potential roadblocks will be crucial for businesses aiming to thrive in an increasingly automated world.
- Technology adoption and integration: One of the most significant challenges is the adoption and integration of new technologies. Many companies, especially small and medium-sized enterprises (SMEs), may struggle with the initial costs and complexity of implementing advanced automation systems. Additionally, integrating new technologies with existing infrastructure can be a daunting task, requiring significant investment in both time and resources. Resistance to change, lack of technical expertise, and concerns about the reliability of new systems can further slow down the adoption process.
- Economic constraints: The financial burden associated with automation, including the cost of new equipment, software, and training, can be a significant barrier for many businesses. Economic uncertainties, such as fluctuations in global markets, can also impact companies' ability to invest in automation. For some industries, the return on investment (ROI) for automation may not be immediately apparent, leading to hesitation in committing to large-scale automation projects.
- Regulatory and compliance issues: As automation becomes more prevalent, regulatory bodies are likely to impose new rules and standards to ensure safety, security, and fairness in the workplace. Navigating these regulations can be complex, particularly for industries operating across multiple jurisdictions with different compliance requirements. Companies will need to stay informed and agile to adapt to changing regulatory landscapes, which may require additional investments in compliance management and legal expertise.
- Workforce displacement and skills gap: The rise of automation also raises concerns about workforce displacement. As machines take over repetitive and manual tasks, there is a risk that certain jobs may become obsolete. This creates a skills gap, where the existing workforce may lack the technical skills required to operate and maintain advanced automation systems. Companies will need to invest in retraining and upskilling programs to help employees transition into new roles that complement automated processes.
- Cybersecurity risks: With the increasing reliance on interconnected systems and IoT devices, cybersecurity has become a critical concern. Automated systems are vulnerable to cyberattacks, which can disrupt operations, compromise sensitive data, and cause significant financial losses. Developing robust cybersecurity measures and staying ahead of emerging threats will be essential to protecting automated infrastructure.
Opportunities for Innovation
Despite these challenges, the future also presents significant opportunities for innovation. New business models and revenue streams will emerge as companies leverage automation to create more efficient and sustainable operations. TEAL is committed to driving innovation in the industry, continuously exploring new technologies and solutions that push the boundaries of what’s possible.
Shaping the Future of Industrial Automation with TEAL
The future of industrial automation is shaped by trends such as the increased adoption of AI and machine learning, the expansion of autonomous systems, and the integration of 5G. While these advancements bring about challenges, they also offer tremendous opportunities for innovation and growth.
At TEAL, we are committed to leading the charge in industrial automation. Our dedication to innovation ensures that we not only overcome the challenges ahead but also seize the opportunities to drive sustainable, efficient, and customized automation solutions.
As we look to the future, we invite you to engage with TEAL’s expertise and solutions. Together, we can overcome the hurdles, seize the opportunities, and shape a smarter, more efficient future for the automation industry.