Harnessing integrated automation for smarter machines
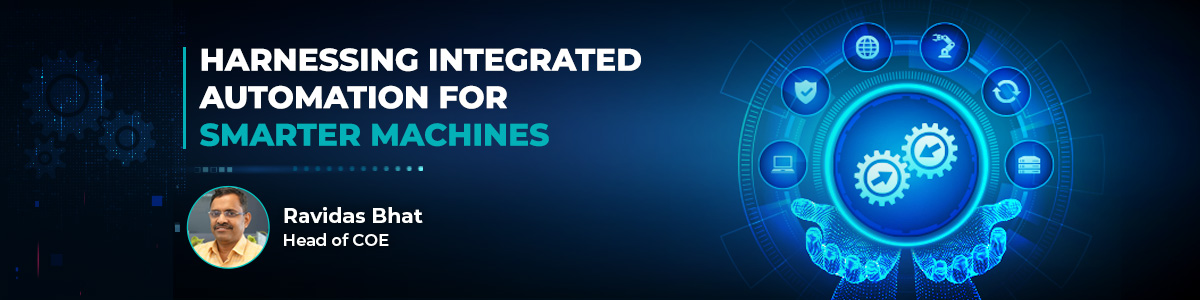
The manufacturing industry is undergoing a significant transformation. We're moving away from isolated, manual processes. Today, factories are stepping into a future powered by the revolutionary concept of integrated automation. This concept connects machines, processes, and data seamlessly, paving the way for a smarter, more efficient production era.
In this blog, we will discuss automation integrated systems, explore their key components, examine the power of data acquisition, and discuss how they work together to shape the future of automation in a data-driven manufacturing landscape.
An Introduction to Integrated Automation
Integrated automation goes beyond simply automating individual tasks. It's the arrangement of a connected ecosystem—where machines communicate with each other, software platforms manage workflows, and data analysis guides continuous improvement. This integrated approach unlocks many benefits, including increased efficiency, improved quality, enhanced flexibility, reduced costs, and data-driven decision-making.
Now, let's discuss about data acquisition.
A Glimpse of Data Acquisition (DAQ)
Data is the fuel that drives modern automation. Data acquisition (DAQ) systems act as the ears of automation, collecting vital data from various sources in a manufacturing environment.
DAQ systems, versatile in their capabilities, can capture data from machine sensors, production lines, and environmental factors. The type of data collected depends on the specific application. This data is then fed into the integrated automation platform for analysis and utilization.
Across various industries, DAQ plays a crucial role:
Automotive: DAQ systems monitor engine performance, test vehicle components, and ensure quality control.
Food & beverage: It helps control ingredient ratios, maintain optimal product temperature, and monitor equipment efficiency.
Pharmaceutical: DAQ systems, with meticulous monitoring, ensure accurate measurement of critical ingredients, monitor environmental conditions, and, most importantly, guarantee product quality.
By collecting and delivering real-time data on various aspects of production, DAQ systems provide immediate and valuable insights for better decision-making and process optimization.
How DAQ and Integrated Automation Software Work Together
Integrated automation software acts as the conductor of the data-driven manufacturing symphony. Leveraging data collected through DAQ systems puts together various aspects of production.
This seamless collaboration between DAQ and integrated automation software fosters a data-driven approach to manufacturing. Manufacturers can optimize their processes, improve efficiency, and achieve higher quality standards through real-time data analysis and automated actions.
Now, let’s learn about data acquisition and integrated automation in detail.
The Power of Data Acquisition: Revealing the Secrets of Our Machines
The world around us is awash in data, and unlocking its potential lies in the power of Data Acquisition (DAQ) systems. These unsung heroes bridge the physical world and the digital realm, capturing critical information from sensors and devices for analysis and decision-making.
There are two main types of DAQ systems:
● Analog DAQ systems: These capture continuous electrical signals and convert them into digital data for computer processing. Think of them as translators, taking the language of voltage fluctuations and transforming it into a language computers can understand.
● Digital DAQ systems: directly capture digital signals from sensors and devices, eliminating the need for analog-to-digital conversion. They're like specialized couriers, efficiently transporting digital information for further analysis.
DAQ Applications: A Journey Across Industries
DAQ systems are the workhorses of various fields:
Research: From monitoring brain activity in neuroscience to tracking climate data in ecology, DAQ systems provide the raw data that fuels scientific discovery.
Environmental monitoring: DAQ systems are crucial in tracking air and water quality, ensuring a healthy planet for future generations.
Manufacturing: Here's where DAQ truly shines. DAQ systems play a critical role in the manufacturing value chain, especially for product improvement and post-warranty analysis through traceability. Here's how:
Leak testing analysis: DAQ captures and analyzes data from leak tests, helping identify weaknesses and improve product design. This translates to fewer leaks and a better customer experience.
Verifiable quality control: Imagine tightening a crucial bolt on a product. A DAQ system linked to a QR code can record the exact torque applied, creating a verifiable record for quality control and future reference. This ensures consistent product quality and aids in post-warranty analysis if necessary.
DAQ in Machine Building
In machine building, DAQ systems are the conductors, orchestrating a symphony of data from various sensors. These sensors track parameters like:
● Temperature: Monitoring temperature variations ensures optimal machine performance and prevents overheating.
● Vibration: Analyzing vibration patterns helps identify potential mechanical problems before they lead to breakdowns.
● Pressure: Monitoring pressure levels in hydraulic systems is crucial for smooth operation and safety.
DAQ: The Skills You Need to Master
To work effectively with DAQ systems, a strong foundation in the following areas is beneficial:
Electronics: Understanding how sensors convert physical phenomena into electrical signals is critical.
Computer programming: The ability to program DAQ software to collect, analyze, and visualize data is essential.
Problem-solving: Interpreting data and troubleshooting challenges encountered during the data acquisition is crucial.
By understanding the power of DAQ systems and possessing the necessary skills, you can unlock the hidden secrets within your machines, leading to better performance, enhanced customer experience, and continuous improvement in various fields.
Integrated Automation Takes Control
Integrated automation represents a revolutionary shift in the way industries manage and optimize their operations. At its core, integrated automation software enables the seamless connection and control of diverse devices and systems, transforming manual processes into efficient, automated workflows. This sophisticated technology is the backbone of modern industrial automation, driving significant efficiency, accuracy, and productivity improvements.
What Integrated Automation Software Does
Integrated automation software is designed to unify and streamline the operation of various devices and systems within an industrial environment. It acts as a centralized platform that can:
● Connect devices: Integrated automation software can establish communication between disparate devices and systems, regardless of their protocols or manufacturers. For instance, it can connect a PLC (Programmable Logic Controller) with a SCADA (Supervisory Control and Data Acquisition) system or a robotic arm with a conveyor belt system.
● Control operations: Manage and coordinate the functioning of all connected devices, ensuring they work harmoniously.
● Monitor performance: Continuously track the performance and status of systems, providing real-time data for analysis.
● Automate processes: Execute predefined tasks and workflows automatically, liberating human resources for more strategic and creative endeavors.
Automating Tasks and Workflows
Integrated automation software excels at automating repetitive and complex tasks. By creating predefined workflows, the software can execute sequences of actions without human intervention. This automation can include:
● Routine operations: Automating daily checks, data logging, and reporting.
● Complex processes: Coordinating multi-step manufacturing processes, such as assembly, testing, and packaging.
● Real-time adjustments: Automatically adjust parameters based on real-time data to maintain optimal performance.
Benefits of Using Integrated Automation Software
The adoption of integrated automation software offers numerous benefits, including:
● Increased efficiency: Automating tasks reduces the time and effort required to perform them, leading to faster operations and higher throughput.
● Improved accuracy: Automation minimizes human error, ensuring precise and consistent execution of tasks.
● Enhanced productivity: By automating routine tasks, your team can liberate their time and energy and focus on higher-value activities that drive innovation and productivity.
● Real-time monitoring: The power of continuous monitoring and data collection empowers you with insights that enable proactive problem-solving and predictive maintenance, ensuring you stay in control.
● Cost savings: By optimizing processes and reducing errors, automation can lead to significant cost reductions in labor, materials, and maintenance.
Examples of Integrated Automation Software Applications
In industrial settings, integrated automation software controls complex manufacturing processes. For example:
● Automated assembly lines: The software coordinates robots, conveyors, and other machinery to assemble products efficiently.
● Quality control: Integrated systems can automatically inspect products using machine vision and other technologies, ensuring high quality.
● Resource management: The software optimizes the use of materials and energy, reducing waste and costs.
What PC-Based Automation Skills are Required for Integrated Automation in Manufacturing
To effectively implement and manage integrated automation in manufacturing, professionals need a robust set of skills, including:
● Technical knowledge: Understanding of industrial automation hardware and software, including PLCs, HMIs, and SCADA systems.
● Networking knowledge: Understanding of industrial communication protocols and network configurations.
● Analytical skills: Ability to analyze data and optimize processes based on insights.
● Problem-solving abilities: Aptitude for diagnosing and resolving technical issues in automated systems.
● Project management: Skills in planning, implementing, and managing automation projects.
By mastering these skills, professionals can leverage integrated automation software to enhance manufacturing operations, driving the industry's efficiency, accuracy, and productivity.
The Perfect Marriage: DAQ and Integrated Automation
Combining Data Acquisition (DAQ) systems and integrated automation software in industrial automation represents a powerful synergy. This union enables precise data-driven decision-making, enhanced process control, and optimized performance, driving significant advancements in various industries, particularly manufacturing.
How DAQ Systems Feed Data to Integrated Automation Software
DAQ systems are designed to collect data from a wide array of sensors and devices that monitor various parameters such as temperature, pressure, vibration, and flow rates. This raw data is crucial for understanding the real-time status and performance of machinery and processes.
The process typically involves:
● Data collection: DAQ systems gather sensor data and convert it into digital signals.
● Data processing: The automation software processes this data, performing real-time analysis to monitor performance and identify anomalies.
● Control and optimization: Based on the processed data, the software can adjust the machinery and processes to optimize performance, reduce waste, and prevent failures.
Real-World Examples of DAQ and Integrated Automation Integration in Manufacturing
Example 1: Machine Performance Optimization
In a manufacturing plant, DAQ systems continuously collect data on machine performance metrics such as spindle speed, motor current, and vibration levels. This data is fed into integrated automation software, which analyzes the information in real-time. If a machine's performance deviates from the optimal range, the software can automatically adjust operating parameters or trigger maintenance protocols to prevent downtime and ensure consistent production quality.
Example 2: Quality Control
DAQ systems can capture data from sensors involved in quality control, such as those measuring product dimensions, weight, or surface finish. Integrated automation software uses this data to immediately identify products that do not meet quality standards and remove them from the production line. This reduces waste and ensures that only products meeting specifications reach customers.
Benefits of This Combined Approach
Data-Driven Decision-Making for Automation
Combining DAQ systems with integrated automation software enables manufacturers to make informed decisions based on real-time data. This data-driven approach allows for precise adjustments and optimizations, enhancing overall efficiency and productivity.
Improved Process Control and Optimization
The integration of DAQ and automation software results in superior process control. Continuous monitoring and real-time adjustments ensure that processes remain within optimal parameters. This improves product quality and reduces resource consumption and operational costs.
Failure Prediction Based on Process Value Deviation
One significant advantage of integrating DAQ systems with automation software is the ability to predict and prevent failures. The software can detect early signs of potential issues by continuously analyzing process data, such as temperature, pressure, or vibration deviations. Predictive maintenance protocols can then be activated to address these issues before they lead to equipment failure, thus reducing downtime and maintenance costs.
The integration of DAQ systems and integrated automation software creates a robust framework for modern industrial operations. This perfect marriage of technology drives innovation and sets the stage for the future of smart manufacturing.
Titan Engineering and Automation Limited (TEAL) is leveraging the power of DAQ and integrated automation to provide turnkey automation solutions to our customers. Continue reading to know how.
TEAL in Action: Delivering Turnkey Solutions with Data Acquisition Expertise
Titan Engineering and Automation Limited (TEAL), India's leading automation solutions provider, takes pride in delivering exceptional turnkey solutions that empower businesses to achieve their manufacturing goals. But what truly sets TEAL apart is its mastery of Data Acquisition (DAQ) systems, transforming data into actionable insights for our customers.
TEAL's DAQ Expertise: The Heart of Turnkey Solutions
At TEAL, we understand that reliable data is the lifeblood of intelligent manufacturing. That's why we go beyond simply providing hardware. Our turnkey solutions seamlessly integrate:
● DAQ hardware: Our team selects and configures the most suitable DAQ hardware for your specific needs, ensuring accurate and efficient data collection.
● Sensors: We integrate a vast array of sensors, from temperature and pressure gauges to vibration monitors, depending on the test requirements of your assembly components.
● In-house developed software: The magic lies in TEAL's software. It seamlessly connects with the DAQ hardware and sensors, transforming raw data into actionable insights.
Unveiling the Power of TEAL's DAQ Systems
Our DAQ systems excel in several key areas:
● Data conversion: They meticulously convert sensor data into clear, digital values, allowing easy analysis and interpretation.
● Sensor integration flexibility: TEAL's DAQ systems are adaptable, seamlessly integrating with various sensor types to cater to your specific component testing needs under assembly.
● Data management and analysis: Our software boasts robust features for:
○ Reliable data storage: We ensure your valuable data is securely stored and readily accessible.
○ Report generation: Generate comprehensive reports with data visualization tools, transforming complex data into easy-to-understand charts and dashboards.
○ MES & ERP integration: TEAL's solutions seamlessly integrate with your existing Manufacturing Execution System (MES) and Enterprise Resource Planning (ERP) systems. This allows for comprehensive data utilization across your entire value chain, unlocking further optimization opportunities.
Benefits of TEAL's Turnkey Approach
By choosing TEAL, you gain a multitude of advantages:
● Streamlined implementation: We provide a single-source solution, ensuring a smooth implementation process.
● Reduced complexity & improved maintainability: Our integrated approach simplifies maintenance and service, keeping your operations running smoothly.
● Enhanced data accessibility and analysis: TEAL empowers you to access and analyze data like never before, unlocking valuable insights.
● Data-driven decision-making: With real-time and historical data readily available through reports and dashboards, you can make strategic decisions based on concrete information.
TEAL: Your Partner in Data-Driven Manufacturing
At TEAL, data is a powerful tool for optimizing operations and achieving manufacturing excellence. With our expertise in DAQ systems and a commitment to turnkey solutions, we're your ideal partner in this data-driven journey.
The Future of Intelligent Automation
Automation is on the cusp of a revolution driven by the relentless rise of advanced technologies like Artificial Intelligence (AI) and Machine Learning (ML). These powerful tools are poised to enhance further the capabilities of Data Acquisition (DAQ) systems and Integrated Automation (IA) software, ushering in an era of intelligent automation unlike anything we've seen before.
How AI and ML Elevate Automation
● Enhanced data analysis: AI and ML algorithms will analyze data collected by DAQ systems with unprecedented depth and speed. This will allow them to identify hidden patterns, predict potential issues, and recommend optimal actions for increased efficiency and productivity.
● Adaptive automation: Integrated automation software will become more adaptive and self-learning. By analyzing historical data and real-time sensor readings, AI-powered integrated automation systems can adjust production processes automatically, optimizing performance based on changing conditions.
● Predictive maintenance 2.0: ML algorithms will take predictive maintenance to the next level. By analyzing trends in DAQ data, they can predict equipment failures and pinpoint the root causes with pinpoint accuracy, leading to more targeted and efficient maintenance strategies.
The Future is Now: Embracing the Power of Intelligent Automation
The future of automation is intelligent, data-driven, and brimming with potential. By embracing technologies like AI and ML, businesses can leverage the combined power of DAQ systems and integrated automation software to unlock a new era of efficiency, optimization, and innovation. The time to invest in intelligent automation is now, and those who do will be shaping the future of their industries.
Ready to Explore the Benefits of DAQ and Integrated Automation?
DAQ systems act as the eyes and ears of your machines, capturing critical data from sensors. Integrated automation software acts as the brain, interpreting this data and translating it into action, optimizing processes and driving efficiency.
The future of automation is powered by data, with AI and Machine Learning further enhancing the capabilities of DAQ and integrated automation. This intelligent automation will unlock greater efficiency, optimization, and innovation potential.
Whether you're in manufacturing, research, or any data-driven industry, DAQ and integrated automation software can revolutionize your operations. Explore how these powerful tools can benefit your specific industry or application and unlock your path to success in the age of intelligent automation.
Frequently Asked Questions