Unraveling the Future with Digital Twin, Industry 4.0 and 5.0
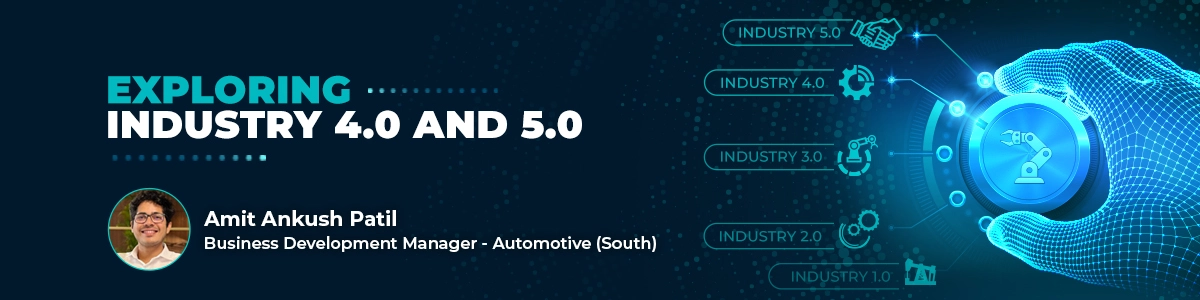
The Industrial Revolution marked a significant era of scientific and technological progress during the 18th century, reshaping predominantly rural agrarian societies into industrialized urban ones. The manufacturing industry has come a long way, progressing through Industry 1.0, 2.0, 3.0, to 4.0, and is now on the cusp of 5.0. With the rise of industrial automation industry, the focus is now on smart manufacturing, AI-driven processes, and interconnected systems, driving the next phase of innovation.
Each of these phases signifies crucial milestones in manufacturing post-Industrial Revolution. One consistent trend has been the diminishing reliance on human labor and an increasing dependence on machinery, which has persisted throughout these phases. Right now, we stand on the brink of what's known as the Fourth Industrial Revolution. Let's delve into what exactly this revolution entails.
The Fourth Industrial Revolution Explained
The Fourth Industrial Revolution, the 4IR or Industry 4.0, encompasses seamless physical, digital, and biological integration. This convergence is driven by progress in artificial intelligence (AI), Internet of Things (IoT), robotics, blockchain, 3D printing, Web3, quantum computing, genetic engineering, and various other technologies. Together, they form the driving force behind numerous products and services rapidly becoming essential aspects of contemporary living.
If we take an example from the manufacturing industry, it would be the industrial equipment now equipped with sensors that monitor performance in real time. This data is analyzed to predict when maintenance is needed, reducing downtime and costly repairs.
Thanks to this remarkable convergence of technological advancements, Industry 4.0 is opening doors to revolutionary shifts in our way of life while significantly shaking up almost every corner of the business landscape. For countless enterprises, Industry 4.0 remains the enticing "next big thing" on their radar or the trend around which they are actively tailoring their strategies. Its essential components encompass automation, big data analytics, virtualization, smart systems, robotization, artificial intelligence (AI), machine learning (ML), and Internet of Things (IoT).
As we witness companies and industries navigating the complexities of the fourth industrial revolution, it's intriguing that the fifth revolution—Industry 5.0—is gaining momentum. However, to embrace Industry 5.0, it's crucial to have a solid understanding of what Industry 4.0 means.
Industry 4.0 and the Emerging Era of Industry 5.0 in India
Industry 4.0 marks a significant shift, blending digital technologies, data exchange, automation, and AI in manufacturing. It ushers in an age of smart factories, where machines interact with each other and humans in real time.
The ripple effect of Industry 4.0 is being experienced worldwide, and India is right in the mix. Recent governmental moves, especially the PLI scheme, have significantly influenced manufacturing investments and productivity. The industry needs to stay vigilant about the revolutionary influence of Industry 4.0 in this sector. If pursued with dedication, Industry 4.0 has the potential to revolutionize manufacturing and propel it to contribute a substantial 25% to the GDP in the foreseeable future."tpci.in"
Industry 5.0 and the Future of Manufacturing
We're witnessing significant changes in how we view and engage with manufacturing and production processes. The seamless incorporation of state-of-the-art technologies marks these changes, causing a profound transformation, impacting the factory floor and entire sectors.
Industry 4.0 and 5.0 mark two clear stages in developing industrial methods, each with unique features and goals. Industry 4.0 hones in on automation, seamless data exchange, and interconnected systems, ushering in the age of smart factories where machines communicate with each other and humans in real time. On the other hand, Industry 5.0 strongly emphasizes the harmonious partnership between humans and machines, striving for a more human-centered and sustainable approach to manufacturing.
In the research paper "sciencedirect.com" titled 'Industry 5.0 – Past, Present, and Near Future' authored by João Barataa and Ina Kayser and published in ScienceDirect, the evolution of Industry 5.0 since 2018 is expounded upon. The diagram delineates the progression from the initial phase (2018-2019 – consequences of digital transformation), elucidating how Industry 4.0 transitioned towards the 5.0 paradigm. The interplay between human-machine interaction (depicted in orange) and technologies (depicted in red) establishes the foundational connections, paving the way for more "social" realms of digitalization, such as customer experience. The subsequent set of papers (2020-2021 – societal priorities for digital transformation) already incorporates sustainability while maintaining a technological underpinning that migrates from Industry 4.0 and delineates the connections to operator 4.0 and society 5.0. The most recent research (since 2022) presents increasingly intricate scenarios, including smart cities and digital twin technology.
The principal streams in the literature on Industry 5.0 are future-oriented and cross-sectoral. While Industry 4.0 primarily focuses on technology, namely the application of digital technologies to address manufacturing challenges and enhance productivity, Industry 5.0 embraces a broader, more comprehensive objective. This entails a shift towards a customer-centric approach and a more human-centered perspective in general.
Digital Twins represent a revolutionary advancement in digital manufacturing, particularly in the ever-evolving landscape of Industry 4.0 and the intriguing developments of Industry 5.0. Continue reading as we delve deeper into this remarkable innovation.
Harnessing the Power of Digital Twins
In the 1960s, NASA developed the concept of Digital Twins to mimic and simulate space missions. Over time, they've transformed into dynamic, information-driven replicas of physical objects, procedures, or systems. Digital Twins have taken off in digital manufacturing by merging IoT sensors, advanced data analytics, and real-time connectivity. This combination has empowered manufacturers to fine-tune their processes, closely monitor equipment health, and predict maintenance requirements with unparalleled precision.
They'll act as bridges, enabling smooth communication and offering instant, valuable insights to inform decision-making. A recent report suggests that the worldwide digital twin market is set to surge from $10.1 billion in 2023 to a staggering $110.1 billion by 2028, with a remarkable CAGR of 61.3% over the forecasted period."marketsandmarkets.com"
Implementing Digital Twins solutions can be expensive, involving substantial investments in various technological components like sensors and software, infrastructure development, maintenance, data quality control, and security measures. However, there are few benefits that the manufacturing industry stands to gain several advantages from integrating Digital Twins into their operations:
- Real-time remote monitoring: Obtaining a comprehensive, real-time view of a complex physical system can be daunting or even infeasible. Digital Twins allow users to access and monitor these systems from anywhere, enabling users to oversee and manage system performance remotely.
- Accelerated risk assessment and production time: Digital Twins empower companies to validate and test their products before they exist. By replicating the intended production process, engineers can spot errors before production. Engineers can also simulate system disruptions, explore unexpected scenarios, and devise corresponding mitigation strategies. This capability not only enhances risk assessment but also expedites new product development while increasing the reliability of production lines.
- Enhanced team collaboration: With 24/7 access and process automation for system data, technicians can allocate more of their focus toward fostering collaboration between teams and improving operational efficiency.
- Predictive maintenance: Digital Twins have IoT sensors that generate large amounts of real-time data. This data can be analyzed to identify issues within the system proactively. This feature enables enterprises to plan predictive maintenance more accurately, improving production line efficiency and reducing maintenance costs.
Moreover, it's anticipated that the use of digital twin technology will experience a significant surge in the coming years. This surge can be primarily attributed to the rapid advancements in AI, Extended Reality (ER), Cloud Computing, and Internet of Things (IoT). Already, various industries have embraced this technology, integrating it into different aspects such as product development, production, and maintenance. Let's explore how harnessing the power of Digital Twins in conjunction with Industry 4.0 and IoT can enhance business operations.
Practical Applications of Digital Twins and Industry 4.0 with IoT
Integrating Digital Twins and Industry 4.0 technologies with IoT is reshaping industries. This dynamic combination offers a range of powerful applications, from predicting maintenance needs to revolutionizing supply chain management. Let's delve into some critical use cases to understand their transformative impact.
Predictive Maintenance: Optimizing Machinery Uptime: Predictive maintenance is a cutting-edge application of digital twins and Industry 4.0 technologies. It utilizes real-time data from sensors and IoT devices installed on machinery and equipment. By analyzing this data, algorithms can predict when equipment will likely fail or require maintenance. This proactive approach enables organizations to perform maintenance tasks precisely when needed, preventing unexpected breakdowns and reducing downtime. This optimization of machinery uptime results in increased productivity, cost savings, and a longer lifespan for equipment.
Product Lifecycle Management: Streamlining Product Development: Product Lifecycle Management (PLM) is a comprehensive strategy that employs digital twins and IoT in developing and managing a product from its inception to its retirement. Digital twins play a pivotal role in this by creating a virtual representation of the product, allowing for detailed analysis and simulations at every stage of development. This facilitates better collaboration among teams, ensures design accuracy, and reduces the time-to-market. It also enables organizations to track and manage product data, configurations, and revisions efficiently, streamlining the entire product development process.
Smart Supply Chain: Efficient Logistics and Inventory Management: Leveraging digital twins and Industry 4.0 principles in the supply chain transforms it into a 'smart' and highly efficient system. By integrating IoT sensors and devices, companies gain real-time visibility into their supply chain operations. This visibility extends from the warehouse to transportation and even the end consumer. It enables precise tracking of inventory levels, allowing for optimized restocking and reduced carrying costs. Moreover, predictive analytics can anticipate demand fluctuations, enabling organizations to make informed decisions about production and distribution.
Quality Assurance: Ensuring Product Excellence: Digital twins and Industry 4.0 technologies revolutionize the quality assurance process by providing a dynamic and virtual representation of the product. Through continuously monitoring real-world performance data, manufacturers can compare it with the digital twin's expected behavior. Any discrepancies can be quickly identified and addressed, ensuring that products consistently meet or exceed quality standards. This level of quality assurance boosts customer satisfaction and minimizes costly recalls and warranty claims.
Virtual Commissioning: Simulating and Testing Production Processes: Virtual commissioning is a pivotal application of digital twins and Industry 4.0 in manufacturing. It involves creating a digital replica of the production environment, including machinery, equipment, and automation systems. This virtual environment allows for rigorous testing and simulation of various production scenarios before implementation. By doing so, companies can identify and rectify potential issues, optimize processes, and fine-tune automation systems without disrupting real-world operations. This significantly reduces the risk associated with commissioning and ensures a smoother transition to full-scale production.
These use cases exemplify how digital twins, coupled with Industry 4.0 technologies and IoT, are revolutionizing various aspects of industries, leading to enhanced efficiency, reduced costs, and improved product quality.
Titan Engineering and Automation Limited (TEAL) is a prominent automation company in India, committed to staying at the forefront of evolving technologies and solutions to propel our customers forward. We specialize in deploying Industry 4.0-enabled solutions, leveraging our distinctive technical capabilities. Curious about where our expertise truly shines? Read on.
TEAL is Leveraging Industry 4.0 to Craft Smart Assembly Solutions
We're all about crafting smart assembly solutions that seamlessly integrate with the cutting-edge world of smart manufacturing. Our suite of smart factory solutions takes a comprehensive approach, providing a clear roadmap for navigating the complexities of Industry 4.0. This means making strategic decisions and offering practical suggestions to make these strategies a reality, including optimizing the lean assembly line for maximum efficiency. The end goal? A tailored connectivity blueprint for your smart factory.
Here's what you can expect when you implement Industry 4.0 in your manufacturing assembly process:
- Deep-dive analytics and valuable insights into machine performance
- Crucial inputs for both research and development, as well as production
- Unparalleled data transparency and real-time monitoring, all the way from the operator level to top management
- A smart, interconnected machine that boasts increased efficiency and unwavering reliability
As part of the Turnkey automation solutions, we've implemented Industry 4.0 integrated solutions for our assembly machines, seamlessly connecting field elements, PLC, SCADA, and Server/Cloud systems. Our Industry 4.0 solutions provide valuable insights into operational and functional management, from the shop floor to top-level management, enabling continuous improvement initiatives.
Here's how it benefits different levels:
- Operator: They work alongside smart machines that enhance their efficiency and ease of operation
- Lower Level Management: They receive real-time data on machine efficiency and timely alerts for predictive maintenance
- Middle-Level Management: They access comprehensive efficiency reports, including machine logs, error logs, and graphical representations for proactive maintenance planning
- Top Level Management: They gain insights into overall plant efficiency, offering valuable guidance for organizational enhancement
We provide tailored Industry 4.0 solutions that perfectly align with our customers' needs. One of our standout offerings is Software as a Service designed for Smart Production Management Systems. This powerful software allows for centralized deployment, enabling the seamless collection of data from shop floor machines, facilitating in-depth data analysis, and streamlining report generation. We're excited to share the exciting initiatives we're undertaking to harness the potential of IoT for our valued customers.
TEAL's Game-Changing IoT Strategies
In an era where technological advancements are shaping the future of industries, TEAL stands at the forefront of innovation with its groundbreaking IoT initiatives tailored for Tier 1 and OEM customers. Among its pioneering projects, TEAL's focus on Battery Pack Assembly Lines, Compressor Motor Assembly Lines, and Fuel Pump Assembly Lines is poised to redefine manufacturing processes.
EV Battery Pack Assembly Lines: Contributing towards Sustainable Transportation: TEAL's foray into EV battery pack assembly lines is visionary. As the world gravitates towards sustainable transportation solutions, TEAL recognizes their critical role in reshaping the automotive industry. IoT integration optimizes these assembly lines for efficiency, precision, and sustainability.
The IoT-enabled system constantly monitors and analyzes various parameters of battery production, from cell voltage and temperature to overall pack health. Real-time data feedback allows immediate adjustments, ensuring each battery pack meets the highest quality standards. Moreover, predictive maintenance algorithms identify potential issues before they escalate, guaranteeing a reliable and long-lasting power source for electric vehicles.
Compressor Motor Assembly Lines: Efficiency Unleashed: TEAL's IoT-enabled Compressor Motor Assembly Lines are a testament to the company's commitment to streamlining assembly operations. By leveraging IoT technology, TEAL enables real-time monitoring of critical parameters such as motor speed, temperature, and power consumption. This ensures precise control over the assembly process, leading to products of unparalleled quality.
Furthermore, integrating machine learning algorithms facilitates adaptive manufacturing, allowing the system to fine-tune operations based on historical data and current conditions. This dynamic approach enhances efficiency and results in cost savings and reduced waste.
Fuel Pump Assembly Lines: Precision Engineering: TEAL's IoT-driven Fuel Pump Assembly Lines exemplify the company's dedication to precision engineering. TEAL ensures that each component is meticulously assembled by integrating IoT sensors and data analytics, meeting the highest industry standards.
Real-time data feedback mechanisms allow immediate adjustments, ensuring that every fuel pump meets the strictest quality criteria. TEAL's predictive maintenance protocols also guarantee uninterrupted operations, reducing the likelihood of unexpected downtime.
TEAL is revolutionizing production processes by pushing the boundaries of assembly through IoT initiatives and setting a new standard for quality and efficiency in the industry. With Battery Pack Assembly Lines, Compressor Motor Assembly Lines, and Fuel Pump Assembly Lines leading the way, TEAL is poised to shape the future of manufacturing for its customers worldwide.
A Glimpse into TEAL’s Future with Advancing Technology
Our IoT initiatives for customers represent a significant leap towards a future where technology and manufacturing seamlessly converge. By embracing IoT, we ensure higher efficiency and precision in assembly processes and future-proofing our solutions in an ever-evolving industry landscape.
As we continue to push the boundaries of what's possible in assembly solutions, it's evident that we are not merely an automation company; we are architects of a new era helping our customers in the manufacturing industry. With IoT solutions at our core, we are poised to shape the future of assembly solutions, setting new benchmarks and inspiring industry-wide transformation.
In conclusion, businesses must embrace the future of manufacturing, which is more pressing now than ever. Integrating cutting-edge technologies such as Digital Twin, Industry 4.0 and 5.0, and IoT solutions marks a pivotal shift towards a more efficient, sustainable, and competitive industrial landscape.
By adopting these transformative tools, businesses can pave the way for a future where production processes are smarter, more agile, and deeply attuned to the needs and demands of an ever-evolving market. Embracing this paradigm shift is not merely an option but a strategic imperative for enterprises looking to thrive in the present and shape a more resilient and sustainable future.
Frequently Asked Questions
Industry 4.0 is revolutionizing India's manufacturing sector, bringing a multitude of advantages:
● Enhanced productivity and efficiency through automation, data analytics, and interconnected systems
● Improved quality control and consistency through real-time data monitoring and predictive maintenance
● Reduced costs and waste minimization through efficient resource management and optimized production planning
● Innovation and creativity fostered by Industry 4.0, enabling new products, services, and business models
● New market opportunities opened up by digitally connected supply chains and enhanced production capabilities
● Global competitiveness strengthened as Indian manufacturers embraced Industry 4.0, offering high-quality products at competitive prices
● Job creation and upskilling driven by demand for skilled workers in emerging technologies
● Sustainable development is promoted through resource efficiency, waste reduction, and energy optimization
Industry 4.0 and Industry 5.0 represent two distinct phases in the evolution of manufacturing, each characterized by unique technological advancements and a different approach to production.
Industry 4.0
- Focuses on automation, data exchange, and interconnected systems to optimize production processes
- Employs technologies like IoT, cloud computing, and big data analytics to enhance efficiency and productivity
- Prioritizes machine-to-machine communication and data-driven decision-making
Industry 5.0
- Emphasizes human-machine collaboration, placing humans at the center of the manufacturing ecosystem
- Leverages artificial intelligence, robotics, and adaptive technologies to augment human capabilities, not replace them
- Promotes personalized production, customization, and sustainability, addressing individual needs and environmental concerns
Industry 4.0 optimizes production through automation and data, while Industry 5.0 seeks a harmonious balance between human ingenuity and advanced technologies, emphasizing social and environmental responsibility.
A digital twin is a virtual replica of a physical object or system continuously updated with real-time data from sensors and other sources. This dynamic representation allows for real-time monitoring, simulation, and analysis of the physical counterpart, enabling optimization, predictive maintenance, and improved decision-making.
Here are some examples of digital twins in various industries:
Manufacturing: A digital twin of a manufacturing plant can simulate production processes, identify potential bottlenecks, and optimize resource allocation.
Product Development: A product's digital twin can test and refine designs, predict performance under various conditions, and identify potential failure points before building physical prototypes.
Healthcare: A digital twin of a patient's heart can simulate the effects of different treatment options and predict potential complications.
The Internet of Things (IoT) encompasses a vast array of devices and applications that connect everyday objects to the Internet, enabling them to collect and exchange data. Here are some notable examples of IoT in action:
Wearable Technology: Fitness trackers, smartwatches, and health monitors collect data on physical activity, sleep patterns, and vital signs, providing insights into personal health and well-being.
Industrial Automation: Connected machines and sensors in factories collect data on production processes, enabling real-time monitoring, predictive maintenance, and optimized operations.