IoT, IIoT, and the transforming industrial landscape
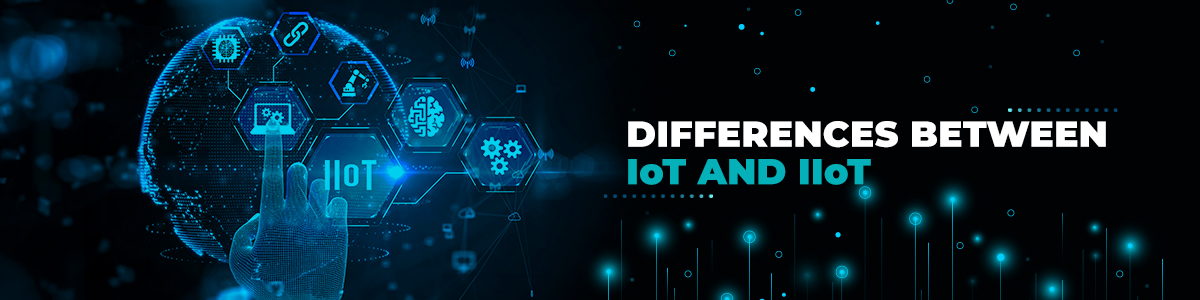
Dubbed ‘Industry 4.0’, the Fourth Industrial Revolution is centered on the use of automation and Artificial Intelligence to drive profits. And the one technology that has become the most powerful symbol of this, our current industrial era, is the Industrial Internet of Things (IIoT).
Amid the unceasing thrust on digitization across sectors, the advantages that IIoT lends to expedite an enterprise’s digitization initiatives has not been lost on the stakeholders, all of whom are scurrying to integrate this innovative technology with their existing production systems. The success of any digital transformation initiative hinges greatly on the efficiency of the systems tasked with managing flow of data. To that end, IIoT-powered technologies can, particularly when installed on the manufacturing floor, create cross-functional channels for exchange of data.
But how is IIoT exactly revolutionizing the modern industry? And how is it so very different from the Internet of Things (IoT) These are a few questions we can answer:
What is IoT?
It is hard to think of a simpler definition for Internet of Things (IoT) beyond the name itself! Connectivity is at the heart of the IoT technology, wherein embedded gadgets and devices, ranging from temperature sensors to smartphones, and even buildings, can share data with each other and human beings once they are integrated with the worldwide web. In the recent past, there has been a proliferation of IoT devices across sectors, with many of us actually using this technology without being aware of it. This could be use of the smartphone to control the speed and temperature of the air-conditioning system, or automated ambient lighting systems. The IoT-powered suite of technologies effectively entails seamless exchange of data, allowing uninterrupted communication between devices to make life easier.
Visualizing an IoT-powered network requires no great leap of the imagination. It is merely an arrangement of an array of devices that could be spread across either a small or large area, or, connected to the internet, be spread across geographically remote locations, each collecting, and sharing data across the network. The embedded devices that are the building blocks of the IoT technology allow for erasure of physical boundaries among the electronic devices, allowing for free communication with each other over the internet.
History of IoT
The term ‘Internet of Things’ was coined by a computer scientist from the United Kingdom called Kevin Ashton at the turn of the century. Although the first reported use of this obviously path-breaking technology can be traced back to the 1980s, it was not until the first decade of the new century that its vast scope of possibilities was unveiled to the world. Even prior to the advent of the smartphone with its touch screens, several leading electronic firms were putting IoT to use to enhance the operations of their products. Some of the notable IoT gadgets in this period included ‘Smart’ fridges, ‘Smart’ fans, among others. But it was the advent of the smartphone that truly announced the IoT to the world.
Over the years, IoT-powered technologies have found applications across sectors, from household appliances to reducing power consumption and carbon emissions at thermal power plants. However, the industrial sector, particularly manufacturing enterprises, requires more complex solutions, driving the evolution of this technology. The Industrial Internet of Things (IIoT) emerged from this need, enhancing efficiency and optimizing automation solutions. This shift aligns with what is industrial automation, which integrates advanced control systems, robotics, and data-driven decision-making to streamline production. Additionally, innovations like the DC-DC converter in EV technology are revolutionizing electric vehicles by ensuring efficient power conversion and improved performance.
What is IIoT?
The Industrial Internet of Things (IIoT) is an advanced subset of the IoT suite of technologies. However, its less sophisticated parent technology is primarily about use of embedded devices and sensors to monitor physical conditions, and collect data on physical parameters. However, the IIoT-powered suite of technologies is geared towards using this data and the established communication channels to achieve tangible results. It was not without reason that the advent of IIoT was said to herald the dawn of a new industrial age – the technologies based on IIoT were primarily geared towards profitability (Science Direct).
At TEAL, we are constantly leveraging the capabilities of IIoT to stay ahead of the curve, and remain future-ready. As an enterprise driven by the desire to constantly reinvent itself, at TEAL, we have tapped into the potential of Industry 4.0 technologies to deliver customized turnkey automated solutions to a number of our clients. Our IIoT-powered networks are tailor-made to meet production requirements, comprising hardware such as programmable logic controllers (PLCs), SCADA devices, connected with our communication network through the cloud (TEAL).
IoT v/s IIoT
Primarily, the difference is functional. Where the IoT-powered suite of technologies is primarily used for data collection, IIoT is geared towards enabling cross-functional communication on the manufacturing floor. For instance, some of the commonest examples of IoT devices that one is likely to spot daily include temperature sensors or fire alarms in a building. These devices are connected to the security system of the structure, and can, on detecting fire, say, trigger an alarm to activate evacuation procedures. IIoT technology, on the other hand, would use the same embedded device, say a temperature sensor, to draw a conclusion on the condition of a machine, and use the information to submit a diagnostic report on the overall condition of the network. As the above example illustrates, IIoT is aimed at using technology towards achieving ‘actionable’ results. More often than not, IIoT devices are used on-site, as opposed to their IoT counterparts, since the former is but a part of a larger production set-up (Science Direct).
Even the network requirements are different for both IoT and IIoT. While even Bluetooth is sufficient for transmission of data collected by IoT devices, ensuring that an IIoT-enabled network functions efficiently requires a network that is vastly superior. To begin with, one of the key benefits of IIoT is its ability to lend real-time visibility of shop floor operations to the management, and achieving this would be next to impossible with standard internet connectivity (Lily Grace).
The other key difference is security requirements. If there is one reason why a number of people, the world over, continue to feel apprehensive over the use of IoT devices, particularly those used for collection and monitoring of personal data, such as an individual’s sugar level or blood oxygen saturation, it is the vulnerability of this information. The security protocols of an IoT network is not robust enough to allay such fears. However, the very nature of the data collected on the manufacturing floor, coupled with their direct impact on operations, necessitates the integration of a much more robust security system (Djibrit Chimere Diaw).
Advantages of IIoT
Although a still-evolving technology, companies are aware of the multitude of possibilities that the use of IIoT can unveil. Prior to the advent of IIoT, most problems arising in a wireless communication network were addressed with ad hoc solutions. However, IIoT allows for seamless integration of advanced communication protocols such as WirelessHART, ISA100.11a in its systems (Science Direct). Among the more obvious benefits of these technologies is that they offer greater flexibility and are more readily adaptable with other networks. Some of the other advantages of using IIoT include
• Achieving greater convergence of Information Communication Technology (ICT) and Operation Technology (OT) domains
• Reduction in both capital and operational expenditure
• Achieving the goal of a ‘Smart’ factory
• Accelerating digital transformation.
Transforming the manufacturing landscape
Previously insulated from each other, IIoT can now integrate the ICT and OT spheres of operation under one functional block, ensuring cross-functional visibility, thereby ensuring improved efficiency across the board. Given that IIoT allows for real-time monitoring of processes, managers can more readily intervene, and revise design plans or production development cycles, thereby enabling a more dynamic set-up.
Among the reasons why IIoT is being as aggressively adopted in the manufacturing sector is the mounting demand for customized products. Meeting these demands will invariably mean having to rejig existing production plants – while the output of each production cycle may be reduced, it is vital to ensure that the throughput rate does not register a proportional decrease.
The use of IIoT, coupled with the convergence of ICT and OT domains, can also help enterprises more systematically and effectively plan modularization of their operations, to sufficiently insulate them from the shocks of disruption in the supply chain. But most importantly for enterprises to fully reap the benefits of IIoT technology, they need to scale up their digital transformation initiatives. Digitizing all production-associated operations can help enterprises put in place efficient data management practices that can, in turn, usher in greater transparency across operations. Digital transformation can also enable enterprises to optimize the advantages resulting from the convergence of ICT and OT; managers would be better placed in such a set-up to identify production bottlenecks and pre-empt problems resulting from the same (Siemens).
Predictive Maintenance is also an example of the ICT-OT convergence that IIoT enables. The ability of ‘Smart’ machines to run regular tests to evaluate their health can generate huge datasets providing a comprehensive report on the overall condition of the machine. This information would then put managers in a position to accordingly plan their production cycles, to ensure that deadlines are met (Siemens).
Challenges
As mentioned earlier, the many advantages of IIoT notwithstanding, it is still a technology that is far from fully evolved. Having to overhaul an existing set-up to make way for one powered by IIoT would invariably entail impacting on a company’s bottom line. For enterprises to offset the cost, it is imperative that they have in their ranks trained technicians not merely familiar with the theoretical aspects of IIoT but well aware of how to use it to drive profitability. At the moment Enterprises will also have to weigh in the possible impact of the IIoT technology on the system’s overall performance.
Future possibilities
Researchers estimate that the IIoT market is likely to be worth USD 11 trillion by 2025 (Science Direct), with many of its hitherto unexplored capabilities, particularly in customer satisfaction, driving this surge in revenue. Given that at the heart of Industry 4.0 is the goal to enable a seamless shift to a digital operational realm, IIoT technology, with its thrust on the use of cyber-physical systems, will continue to define the operational paradigms across industries. These cyber-physical systems can potentially revolutionize manufacturing through the use of embedded devices that connect the manufacturing floor with the physical environment.
Advances in edge computing, and quantum computing, promise many a micro-revolution within the scope of Industry 4.0, with the future of not just the manufacturing sector, but various others, shifting more and more towards ‘autonomous’ from ‘automated’ operations.
Frequently Asked Questions