How automation is benefiting industries
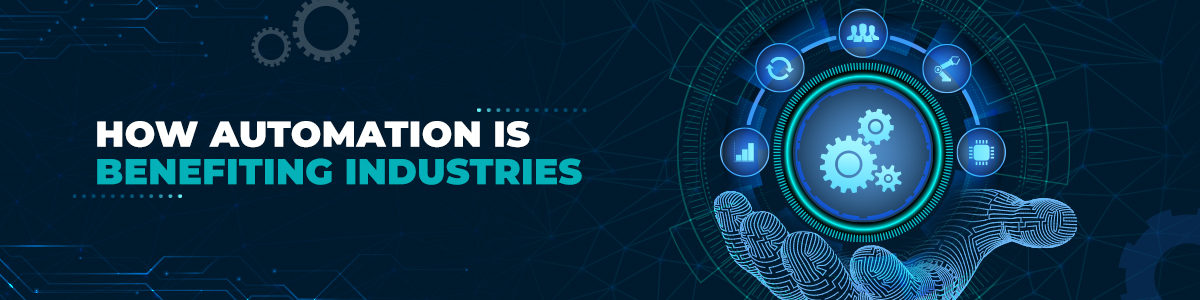
Automation is the only constant; this is the mantra several industries follow. Businesses from all sectors around the world have turned to automation in search of increased efficiency and productivity. It has already become a disruptive force, reshaping industries worldwide due to its benefits, which include streamlined processes, shorter lead times, and better resource utilization. As we look ahead, the future of automation promises even greater advancements, driving innovation and transforming the way industries operate.
In fact, data from Fortune Business Insights projects the global industrial automation market to increase to an impressive 296.70 billion dollars by 2026, indicating a marked shift in business operations. (globenewswire)
While much has been said about industrial automation's rapid global growth, it is crucial that emerging and established businesses also understand its benefits.
Automation landscape in India
It would be an understatement to say that Indian industries are leading the way in adopting automation in their business operations. According to the IDC APJ Automation Survey data, 84% of Indian organizations will scale up their RPA (Robotic Process Automation) initiatives or achieve an enterprise-wide RPA deployment by 2025. (financialexpress)
Manufacturing, healthcare, energy, life sciences, and automotive are some of the country's sectors progressively adopting automation, showcasing a commitment to staying competitive in the global market.
How does automation cause synergy in industrial evolution?
The adoption of automation has sparked some trends that are revolutionizing the way industries work.
Industrial Internet of Things (IIoT)
Automation paved the way for the Industrial Internet of Things (IIoT) by generating massive amounts of data via sensors and control systems. The connectivity and communication infrastructure created for automation became the foundation of IIoT networks, allowing for seamless data exchange. Intelligent devices integrated into automated systems paved the way for similar devices in the IIoT landscape, which serve as critical edge nodes. Automation's real-time monitoring and adaptive capabilities influenced the IIoT's real-time analytics and predictive features, transforming industries with unprecedented connectivity, data insights, and intelligent decision-making. IIoT benefits businesses by increasing efficiency, predictive maintenance, and data-driven optimization.
Smart Factories
Automation has accelerated the evolution of smart factories, seamlessly integrating technology and manufacturing. Automated systems with sensors and data analytics enable real-time monitoring and decision-making in manufacturing processes. These advancements have resulted in smart factories, where interconnected devices communicate to improve efficiency and streamline operations. Smart factories leverage automation's foundation to implement technologies like the Industrial Internet of Things (IIoT), artificial intelligence, and robotics. The integration of these elements results in agile, responsive manufacturing ecosystems. As smart factories continue to evolve, they are poised to revolutionize industrial development by enhancing productivity, minimizing downtime, and fostering innovative, data-driven approaches to production and supply chain management.
Industry 4.0
Automation has been the driving force behind the shift to Industry 4.0. Initially based on automated processes, Industry 4.0 expands on this foundation by incorporating digital technologies into industrial environments.
Industry 4.0 uses the Industrial Internet of Things (IIoT), artificial intelligence, deep learning, and advanced analytics to leverage data collected by automated systems.
This allows us to benefit from real-time insights, predictive maintenance, and adaptive manufacturing processes, which will revolutionize industrial development. Automation ensures that manufacturing is smart, connected, and autonomous, which leads to increased efficiency, lower costs, and greater agility in responding to market demands.
How do we do automation in TEAL?
TEAL, at the forefront of automation technology, offers cutting-edge solutions tailored to diverse industry needs. This enables us to enhance our assembly line solutions capabilities.
Fully Automated Assembly Lines
With state-of-the-art capabilities, TEAL’s fully automated assembly lines are designed to minimize human intervention and maximize efficiency. The assembly lines at TEAL are equipped with linear and rotary transfer systems that ensure fast, stable, and accurate production flow. They offer complete traceability of parts and processes and incorporate the latest industry automation systems and trends into their solutions.
Semi-Automated Assembly Lines
Striking a balance between manual and automated processes, semi-automated assembly lines from TEAL optimize efficiency while allowing for human intervention wherever necessary. Designed to reduce human intervention while still providing flexibility in the assembly process, these systems integrate automation in assembly line with pick-and-place units and walking beam mechanisms, ensuring fast, stable, and accurate production flow.
TEAL’s semi-automated assembly lines are designed to provide a cost-effective solution for small to medium-sized production requirements. These lines allow for the traceability of parts and processes and offer the advantages of the latest cutting-edge technologies.
Advantages of automation
1. Increased efficiency
One primary reason businesses are rapidly adapting to automation is heightened efficiency. By integrating intelligent systems, production processes are streamlined, resulting in faster and more efficient operations. Automation in IT industries optimizes workflows, reduces the number of bottlenecks, and ultimately enhances overall output.
2. Precision and accuracy
A significant merit of automation is its capacity to ensure precision and accuracy in manufacturing processes. Automated systems execute tasks with consistent precision, minimizing errors and elevating the quality of the end product. High quality of products and accuracy in solutions ensure higher customer satisfaction and retention and, ultimately, an increase in business.
3. Cost reduction
Beyond efficiency gains, automation delivers substantial cost reductions as well. Businesses can cut operational costs in the long run by reducing dependency on manual labor. According to a post on RoboticsBiz, industrial automation can lead to increased productivity, reduced labor costs, and improved worker safety. Automation also enables firms to produce goods and products at lower costs, which enables them to scale up.
By increasing productivity, automation can free up budgets and allow a company to redirect profits to other areas. It also lowers the costs associated with hiring and training workers.
4. Longer operating hours
Automation works around the limitations of human-operated production lines by enabling more extended operations. Automated systems can provide even continuous production cycles, reducing downtime and maximizing output efficiency without human intervention.
Challenges in implementing automation
Even as automation brings many advantages, adopting industrial automation comes with several challenges organizations need to navigate. These challenges include:
High initial costs: Especially for smaller businesses setting aside a budget for automation, implementing automation systems comes with a substantial upfront investment in technology, equipment, and training.
Complex implementation: Integrating automation into existing processes can be difficult and require significant changes to workflows and infrastructure. It also entails carefully considering employee training and communication strategies to ensure a smooth transition and reap all the benefits of automation.
Workforce reskilling: Automation often necessitates a shift in the skills required from the workforce, leading to the need for training and reskilling programs.
Cybersecurity concerns: The increased connectivity of automated systems raises cybersecurity concerns, necessitating solid measures to protect against potential threats.
Resistance to change: Employees may resist the adoption of automation due to fear of job loss or a lack of understanding about the benefits it brings. Investment in their reskilling can enable businesses to overcome this challenge.
Maintenance and downtime: Automation systems, like any other technology, require regular maintenance, and unplanned downtime can have a negative impact on productivity.
Customization challenges: Industries with unique or specialized processes may struggle to find off-the-shelf automation solutions that meet their specific requirements.
Lack of standardization: The absence of standardized protocols and technologies in automation systems can impede interoperability and cause compatibility problems.
In conclusion, automation provides numerous benefits, ranging from increased efficiency and precision to significant cost savings. As India positions itself at the forefront of this technological wave, the transformative power of automation is revealed. The country's industrial landscape is on the verge of revolution, contributing to local progress and playing an essential role in the global story of industrial evolution. By adopting automation, India is not only keeping up but also paving the way for a new era of unparalleled efficiency and innovation.
Frequently Asked Questions