Benefits of Turnkey Automation in the Automotive Industry
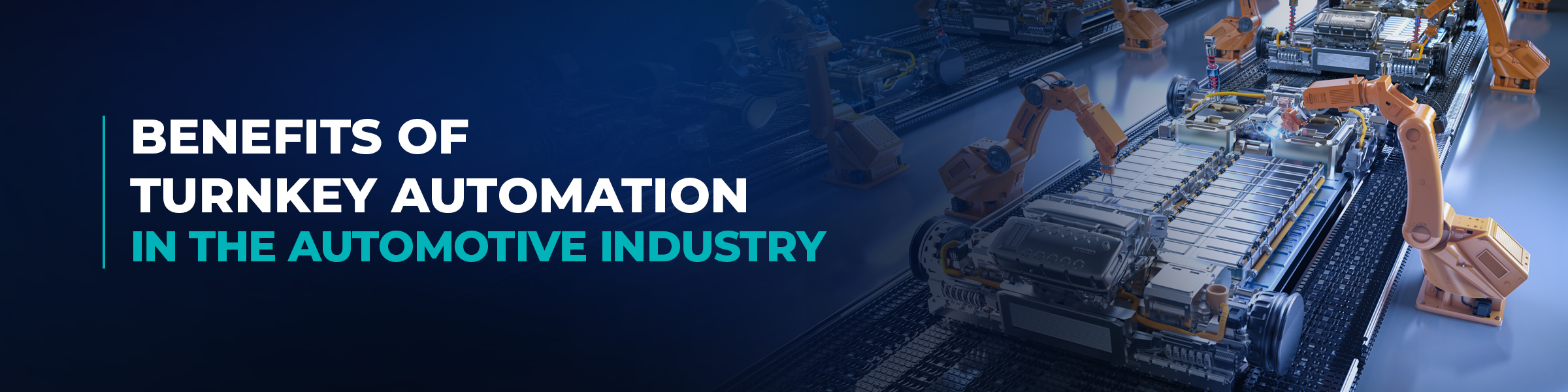
Imagine running an automotive production line where each process is perfectly synchronized, errors are minimized, and output consistently meets the highest quality standards—all without the headache of managing multiple suppliers and integration challenges. That’s the promise of turnkey automation solutions and the future of automation.
The automotive industry is undergoing rapid transformation, with fierce competition pushing manufacturers to deliver high-quality vehicles faster and at lower costs. However, traditional automation approaches involving separate vendors for design, equipment, and installation often result in longer lead times, higher costs, and operational complexity. This is where turnkey automation steps in—offering an all-in-one solution to handle everything from system design to final commissioning, helping automotive manufacturers streamline production while staying competitive.
In this blog, you’ll learn the key benefits of turnkey automation in the automotive sector, how it simplifies complex manufacturing processes, and why it's becoming the go-to choice for forward-thinking manufacturers.
What is Turnkey Automation?
Turnkey automation is a comprehensive solution where a single provider handles the entire automation process—from concept design, engineering, and equipment procurement to system integration, installation, and commissioning. Unlike traditional automation projects, which often require coordinating multiple vendors and managing different stages separately, turnkey solutions offer a single point of contact and responsibility.
In the context of the automotive industry, turnkey automation can cover everything from robotic assembly lines and conveyor systems to quality inspection units and packaging systems. The goal is simple: to provide a ready-to-operate solution fully customized to meet the specific production requirements of automotive manufacturers.
Key features of turnkey automation include:
- End-to-end management: One provider oversees every phase, ensuring seamless integration.
- Customized solutions: Systems are tailored to the manufacturer’s unique production lines and objectives.
- Faster deployment: Since the entire process is handled by one team, the timeline is often shorter than that of piecemeal approaches.
By eliminating the complexities of dealing with multiple vendors and ensuring tight coordination across all phases of automation, turnkey solutions make it easier for manufacturers to adopt advanced technologies without unnecessary delays or risks.
Core Benefits of Turnkey Automation in Automotive
The automotive industry operates in a high-demand environment where precision, efficiency, and flexibility are key. Turnkey automation offers several distinct advantages over traditional automation methods. Here’s how it benefits automotive manufacturers:
Reduced complexity: Managing multiple suppliers, coordinating different teams, and integrating various systems can be a logistical nightmare. With turnkey automation, a single provider manages everything from start to finish, drastically reducing the complexity for automotive manufacturers. This unified approach ensures smoother communication, fewer errors, and faster issue resolution.
Example: Instead of sourcing robots from one supplier and conveyor systems from another and then hiring a third-party integrator, you receive a complete, pre-integrated solution ready to operate.
Faster implementation: Turnkey automation significantly reduces the lead time for setting up a production line. Since all components are designed, built, and tested by one provider, implementation is quicker and more efficient.
Why this matters: In the highly competitive automotive industry, being first to market with a new model or assembly technology can provide a critical edge. Faster deployment means you can ramp up production quickly and meet market demand without delays.
Improved quality and precision: Turnkey systems are designed to ensure optimal performance, minimizing the risk of production errors. Because everything is pre-tested and fine-tuned before delivery, you get a reliable solution from day one.
Impact: Better quality means fewer recalls, lower defect rates, and improved customer satisfaction—crucial for automotive brands striving to build long-term trust.
Cost savings in the long run: While turnkey solutions may require a higher initial investment, they offer long-term cost savings by reducing downtime, minimizing integration issues, and ensuring consistent production quality. Additionally, with a single provider handling maintenance and support, ongoing operational costs are easier to manage.
Fact: A well-integrated turnkey system can help reduce waste, improve energy efficiency, and optimize resource usage, lowering operational expenses.
Scalability and Flexibility of Turnkey Systems
One of the key concerns for automotive manufacturers is whether medical automation solutions can adapt to evolving production needs. As vehicle models become more complex and market demand shifts, manufacturers require systems that can grow and change without disrupting operations. Turnkey automation solutions, coupled with energy automation solutions, are designed with scalability and flexibility in mind, making them ideal for such dynamic environments.
Scalability
- Growing with your business: Turnkey systems are built to accommodate future expansions. Whether you need to increase production capacity, introduce a new vehicle model, or add new processes, scalable turnkey solutions can handle these changes with minimal disruption.
Example: A turnkey robotic assembly line can be easily upgraded with additional robotic arms or adapted for different assembly tasks without requiring a complete overhaul. This ensures that your investment remains valuable as your production needs grow.
Flexibility
- Adapting to different models and processes: Modern automotive plants often produce multiple vehicle models on the same line. Turnkey automation solutions are designed for high flexibility, enabling quick reconfiguration or reprogramming for different tasks. This helps manufacturers maintain agility in response to market trends.
- Why this matters: Flexibility is critical in an industry where frequent model updates are the norm. A flexible turnkey system allows manufacturers to introduce new models faster, staying ahead of competitors.
- Seamless integration with existing systems: Turnkey automation doesn’t mean starting from scratch. Leading providers ensure their solutions integrate seamlessly with your existing infrastructure, whether legacy machines or modern ERP systems.
Result: This reduces downtime during implementation and ensures that your production line runs efficiently without needing a complete overhaul.
TEAL’s Approach to Turnkey Solutions
At Titan Engineering and Automation Limited (TEAL), we understand that turnkey automation is not just about providing equipment—it’s about delivering a complete, reliable, and future-proof solution tailored to your needs. With years of experience in the automation industry, TEAL has developed a comprehensive approach to ensure that our turnkey solutions drive real value for automotive manufacturers.
Comprehensive consultation and customization: We begin by deeply understanding your production requirements, existing infrastructure, and future goals. Our team collaborates with you to design a solution that integrates seamlessly with your current processes while ensuring scalability for future expansions.
Why this matters: No two automotive plants are alike. TEAL ensures that the solution you receive is not a one-size-fits-all package but a custom-tailored system that meets your exact needs.
End-to-end project management: From the initial concept to final commissioning, TEAL manages every aspect of the project. This includes design, equipment sourcing, software development, system integration, testing, and on-site installation.
Benefit: By acting as a single point of contact, we eliminate the complexities and risks associated with coordinating multiple vendors, ensuring a faster and more efficient implementation process.
Advanced technology and quality assurance: TEAL leverages the latest robotics, sensors, and control systems to deliver cutting-edge solutions. Each system undergoes rigorous testing and quality checks before deployment, ensuring it performs at peak efficiency from day one.
Example: For one of our automotive clients, TEAL implemented a robotic welding solution that reduced cycle times while improving weld precision and consistency.
Ongoing support and maintenance: Our commitment doesn’t end at commissioning. TEAL offers comprehensive after-sales support, including regular maintenance, system upgrades, and remote monitoring to ensure long-term reliability and performance.
Result: This proactive approach helps minimize downtime and maximizes the return on your investment, ensuring that your production line remains efficient and productive over time.
Why Turnkey Automation is a Smart Move for Automotive Manufacturers
Staying competitive in this industry requires more than quality products—it demands efficient production, reduced downtime, and the ability to quickly adapt to changing market demands. Turnkey automation solutions offer a clear path to achieving these goals by simplifying the automation process, reducing complexity, and delivering scalable, flexible systems that enhance production efficiency.
By partnering with a trusted provider like TEAL, automotive manufacturers gain access to a fully integrated solution backed by years of industry expertise, advanced technology, and end-to-end project management. Whether you’re looking to improve product quality, reduce costs, or speed up your time-to-market, turnkey automation ensures that your production line operates at peak performance with minimal hassle.
Investing in turnkey automation is a strategic move that positions your business for long-term success in an increasingly competitive landscape.