Enhance Efficiency & Precision with TEAL’s Welding Automation Solutions
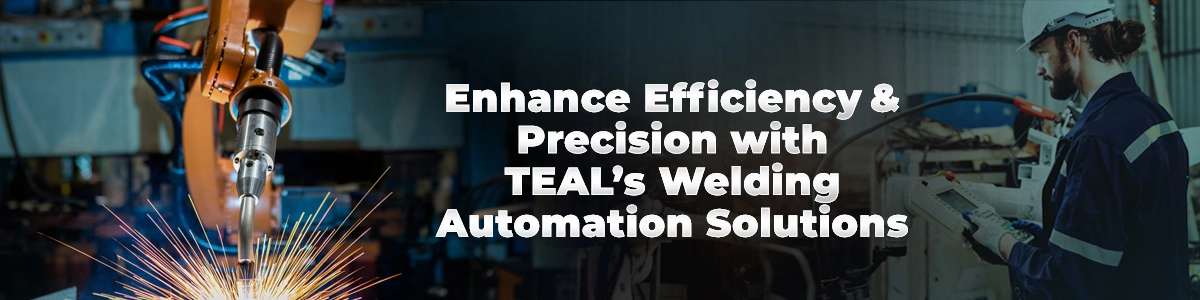
Contents
- 1 The importance of welding automation solutions in manufacturing processes
- 2 Understanding welding automation solutions
- 3 TEAL's expertise in welding automation solutions
- 4 How TEAL consistently delivers superior welding automation solutions
- 5 Key benefits of TEAL's welding automation solutions
- 6 TEAL’s future trends and innovations in welding automation solutions
- 7 Unlock your business's full potential with TEAL’s welding automation solutions
- 8 Frequently Asked Questions
In today's rapidly advancing industrial landscape, welding automation solutions have emerged as a game-changer for manufacturers seeking to enhance productivity, precision, and cost-effectiveness. Titan Engineering and Automation Limited (TEAL) is a renowned company that provides cutting-edge welding automation solutions. TEAL offers comprehensive solutions that revolutionize the welding process for various industries, from robotic welding systems to intelligent welding software. In this blog, we will explore the advantages of welding automation and how TEAL's expertise shapes the future of manufacturing through its innovative solutions. Let’s dive in.
The importance of welding automation solutions in manufacturing processes
As a trusted name in engineering automation, TEAL strives to revolutionize our customers' manufacturing processes, enabling them to achieve remarkable gains in efficiency and precision. By harnessing the power of automation, welding processes can transcend the limitations of manual labor, allowing businesses to unlock a new era of productivity. TEAL understands the importance of welding automation and has developed innovative solutions to address the industry's challenges head-on.
Understanding welding automation solutions
Manual welding often suffers from human errors, resulting in inconsistencies, weld defects, and rework. Moreover, the labor-intensive nature of welding operations can lead to high costs, reduced throughput, and potential safety hazards. These challenges emphasize the need for welding automation to overcome limitations and enhance manufacturing processes.
This is where welding automation comes in. This advanced solution refers to using automated systems, such as robots and advanced control technologies, to perform welding tasks in manufacturing processes. It replaces or assists manual welding operations, providing numerous advantages to industries. By automating welding processes, companies can achieve higher productivity, consistency, and efficiency while maintaining superior quality.
Welding encompasses various techniques, each suited to specific applications. Some common types of welding include arc welding, resistance welding, laser welding, and electron beam welding. Each method has its strengths and limitations, and TEAL specializes in developing automation solutions tailored to different welding techniques. Let’s go through the expertise of TEAL.
TEAL's expertise in welding automation solutions
TEAL is a pioneering company specializing in engineering automation solutions. With years of experience and a diverse portfolio of successful projects, we have established ourselves as a trusted partner for businesses seeking innovative automation solutions. Our expertise extends across various industries, and we pride ourselves on delivering tailored solutions to meet our client's specific needs.
At TEAL, welding automation is at the core of our expertise. We have honed our skills and knowledge to become industry leaders in providing welding automation solutions. Our expert team has extensive experience designing, integrating, and optimizing automated welding systems across different welding techniques and applications.
We possess extensive expertise in welding various metals, including steel, alloys, aluminum, stainless steel, and copper. We have developed specialized automation systems that cater to non-metals weldings, such as plastics and polymer parts. These systems utilize heated probes and ultrasonic joining technology to ensure efficient and precise welding processes.
Our proficiency extends to welding sheets and wires of various sizes, ranging from as small as a human hair to a thickness of 3 millimeters. This allows us to tackle welding tasks with precision and versatility.
Some of our notable success stories include-
Laser welding: In a single pass, we accomplished the laser welding of circumferential edges of 12 tubes, each measuring a mere 0.25mm in thickness. This achievement demonstrates our capability to handle delicate and precise welding operations.
TIG and Plasma welding: We have expertise in TIG and Plasma welding of aluminum tubes with aluminum die-cast housing under controlled environments. These processes ensure no deformation or eroding of the tubes, guaranteeing high-quality welding results.
Robotic TIG welding: Our robotic TIG welding solutions incorporate path trace functionality, enabling us to perform multi-profile welding with exceptional accuracy and consistency.
Resistance welding: We have successfully executed resistance welding of alloy steel using electrodes with a diameter of 1mm and heavy capacity welding up to 500KVA with a diameter of 65mm. This demonstrates our ability to handle intricate welding tasks with precision and efficiency.
Ultrasonic welding: Our expertise in ultrasonic welding spans various industries, including automotive (steering garnish, switches, light clusters) and consumer electronics (medical products, electric toothbrushes). This technique is renowned for achieving clean and high-quality welds, making it a popular choice for joining thermoplastic injection-molded components.
During ultrasonic welding, a welding horn generates vibrations that melt the thermoplastic material at the joint line. The components to be joined are securely held together under pressure while subjected to vibrations, typically at frequencies of 20 or 40kHz. This process ensures strong and reliable bonds between the materials.
Cold metal transfer welding (CMT): We employed CMT welding for the first time, achieving a successful bond between metal sheets of varying thicknesses. The technology effectively prevented deformation by carefully selecting the appropriate metal composition, temperature, and cooling gas. This breakthrough has revolutionized our ability to enhance our customers' value.
TEAL continually strives to deliver superior welding solutions backed by our expertise and commitment to excellence. Want to know how we do it? Keep reading!
How TEAL consistently delivers superior welding automation solutions
TEAL stays at the forefront of technological advancements to deliver top-notch automation solutions. We leverage the latest technologies, including advanced robotics, intelligent control systems, and state-of-the-art welding equipment. Our highly skilled engineers and technicians combine their expertise with these tools to develop and implement efficient and reliable welding automation solutions.
Our knowledge of welding automation covers a wide range of applications and welding techniques. Whether it's arc welding for heavy fabrication, precision laser welding for intricate components, or resistance welding for assembly lines, we have the experience to provide comprehensive automation solutions tailored to the specific requirements of each industry and application.
Key benefits of TEAL's welding automation solutions
TEAL's welding automation solutions are designed to enhance efficiency in manufacturing processes. Automating welding tasks enables businesses to achieve higher productivity and throughput. Our solutions optimize cycle times, reduce idle periods, and ensure continuous and efficient welding operations.
Robotic welding systems offered by TEAL play a pivotal role in achieving high-speed, continuous welding with minimal downtime. These advanced systems can handle complex welding tasks with precision and speed, increasing efficiency and improving overall output. By automating the welding process, businesses can significantly reduce production time and increase overall operational efficiency.
Integrating TEAL’s advanced robotic control and vision systems with our welding automation solutions ensures unmatched precision and repeatability. These systems enable real-time monitoring and feedback, allowing for precise control of welding processes. By leveraging robotic vision systems, we enhance welding operations' accuracy, adaptability, and flexibility.
TEAL prioritizes worker safety through its welding automation solutions. Automating welding processes minimizes human exposure to hazardous welding environments, reducing the risk of accidents and health issues. Our systems are designed to handle challenging welding tasks, allowing operators to work from a safe distance and mitigating the potential dangers associated with manual welding operations.
Automation brings significant ergonomic benefits to the workplace. TEAL's welding automation solutions reduce physical strain on workers, as automated systems perform repetitive and labor-intensive welding tasks. By relieving operators of these burdensome tasks, we improve working conditions, reduce fatigue, and create a safer and more comfortable environment.
TEAL's welding automation solutions drive cost savings through various avenues. Businesses can optimize workforce allocation and reduce labor costs by reducing the need for manual labor in welding operations. Moreover, automation enhances operational efficiency, reducing errors and eliminating rework. These improvements result in significant cost savings for businesses.
In the long run, TEAL's welding automation solutions provide substantial benefits by minimizing rework, material waste, and overall production costs. Automation reduces the need for rework and scrap by ensuring consistent weld quality, saving valuable resources. Additionally, precise control of welding parameters optimizes material utilization, reducing waste and associated costs. These cumulative benefits make automation a cost-effective investment for businesses.
TEAL’s future trends and innovations in welding automation solutions
TEAL acknowledges the importance of staying ahead of emerging trends in welding automation. Collaborative robots (cobots), which work alongside human operators, are gaining prominence, enhancing flexibility and productivity. Machine learning and artificial intelligence revolutionize welding processes by enabling adaptive control systems and predictive maintenance, improving efficiency and quality.
TEAL is committed to continuous innovation and staying at the forefront of technological advancements in welding automation. We invest in research and development to integrate the latest technologies into our solutions. By embracing emerging trends and exploring new possibilities, we ensure that our clients benefit from state-of-the-art automation solutions that address their evolving needs.
Unlock your business's full potential with TEAL’s welding automation solutions
TEAL is dedicated to providing innovative and efficient welding automation solutions that address the changing needs of the manufacturing industry. We combine our expertise, cutting-edge technologies, and a customer-centric approach to deliver tailored solutions that drive productivity, quality, and safety. With TEAL as your partner, you can navigate the industry's challenges and achieve sustainable growth.
We invite you to explore TEAL's comprehensive range of welding automation solutions. Whether you require automation solutions for arc welding, laser welding, or any other welding technique, our team is ready to assist you. Contact us today to learn how TEAL's welding automation solutions can transform your manufacturing processes and help your business thrive in a highly competitive market.